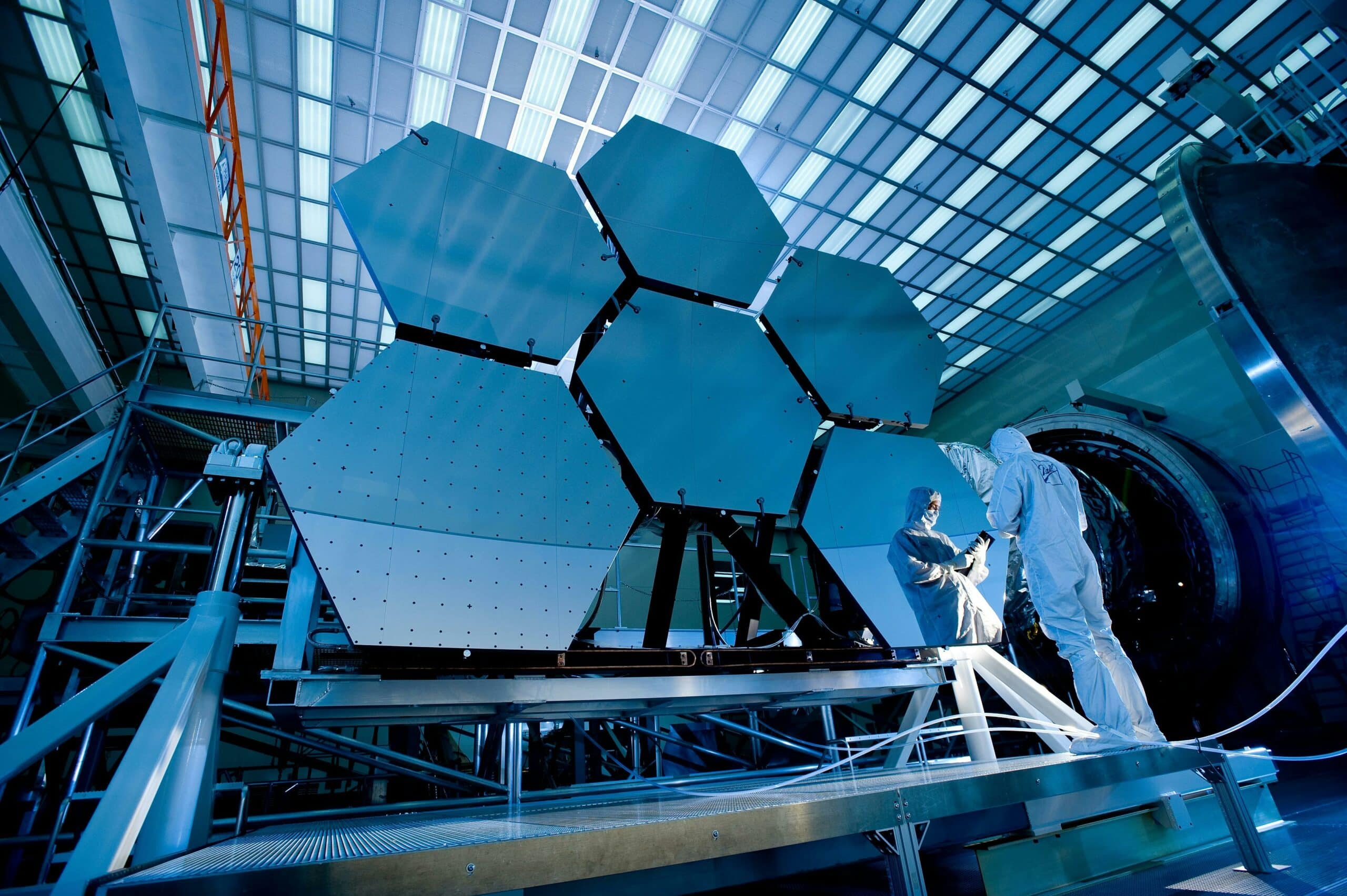
The 10 technological innovations revolutionizing Industry 4.0
Share this article
Contents
Share this article
10 new technologies at the heart of Industry 4.0
Technological evolution is profoundly redefining the industrial sector, combining automation, interconnection and data intelligence. Thanks to these advances, factories and warehouses are becoming more efficient, flexible and precise in their processes.
This article highlights 10 major innovations that are revolutionizing safety, production, logistics and resource management.
1. Connected Objects (IoT): connecting machines for optimized production
TheIndustrial Internet of Things (IIoT) is based on a network of intelligent sensors connected to machines and production infrastructures. These sensors collect, transmit and analyze data in real time, enabling better control of industrial processes.
IIoT makes it possible to continuously monitor equipment status, reduce unplanned downtime and optimize resource management. The integration of this technology contributes to greater energy efficiency, lower operating costs and improved product quality.
Use cases
Real-time monitoring of production and machine performance.
Preventive maintenance through analysis of sensor signals.
Advanced process automation based on collected data.
2. Artificial intelligence and machine learning: towards a predictive industry
Artificial intelligence (AI) and machine learning enable systems to detect trends, anticipate anomalies and make autonomous decisions based on processed data.
They play a key role in predictive maintenance, by analyzing breakdown history and machine behavior to prevent malfunctions before they occur. They are also used to improve inventory management andproduction line optimization.
Use cases
- Optimize production by adjusting parameters according to real-time performance.
- Anomaly detection to prevent production stoppages.
- Automated quality control using computer vision algorithms.
Indoor geolocation relies on technologies such as Bluetooth Low Energy (BLE), Wi-Fi, RFID or Ultra Wideband (UWB) to precisely track the position of equipment and employees in factories or warehouses. Unlike GPS systems, which are ineffective indoors, these technologies enable real-time tracking of industrial assets, improving logistics flow optimization, productivity and worker safety.
Among existing solutions, Wheere stands out as the only one capable of penetrating 50 meters of concrete. Its patented technology makes it possible to cover an industrial site or logistics complex with just four transmitting antennas. Thanks to this breakthrough, companies can locate their assets and teams with an accuracy of less than 1 meter, even in environments where other technologies reach their limits.
Use cases
- Optimize logistics flows by identifying the location of goods in real time.
- Protection of the lone worker PTI by reducing intervention time in the event of an accident, thanks to the precise location of teams.
- Asset tracking to reduce loss and theft of equipment.
4. The Digital Twin: a virtual replica for optimized management
The Digital Twin is a virtual replica of an industrial object, system or process. Thanks to IoT sensors and advanced computer models, this technology makes it possible to simulate, analyze and optimize a piece of equipment or a production line in real time, without physically intervening on the installation.
Digital twins are particularly useful for anticipating failures, testing improvements before they are implemented, and optimizing resource utilization. This approach cuts costs, improves performance and reduces operational risks.
Use cases
- Optimization of production lines by simulating different scenarios before their actual application.
- Reduce downtime by testing technical adjustments without impacting production.
- Operator training in a simulated environment with no risk to real equipment.
5. 3D printing: agile, optimized production
Additive manufacturing, also known as3D printing, revolutionizes traditional production methods by enabling objects to be created by adding material layer by layer from digital files. Unlike subtractive processes such as machining or casting, this approach significantly reduces waste and offers greater design freedom, making it easier to create complex geometries and customize products to meet specific customer needs.
It offers flexibilityby enabling the production of customized parts without the need for costly tooling. It also considerably speeds up development of prototypes and the manufacture of complex components, paving the way for innovative designs impossible with traditional methods.
Use cases
- Customized production without costly tooling.
- Reduced development time for new products.
6. Collaborative robots (cobots): flexible automation
Cobots, or collaborative robots, are designed to work alongside humans, unlike traditional industrial robots which operate autonomously in confined areas. Thanks to advanced sensors and intelligent vision systems, they interact safely with operators, while optimizing repetitive or tedious tasks.
This man-machine collaboration improves the precision of operations, while reducing employee fatigue and optimizing productivity. Cobots are particularly useful in diverse production environments, where flexibility is essential.
Use cases
- Simplification of theassembly processand precision assembly.
- Reduced drudgery associated with repetitive and physically demanding tasks for operators.
7. Augmented and virtual reality: immersive tools for industry 4.0
Augmented reality (AR) and virtual reality (VR) are transforming the industrial sector by offering immersive solutions for training, maintenance and precision assembly.
With augmented reality, technicians can superimpose digital information (schematics, instructions, sensor data) directly onto the equipment they are handling, reducing errors and speeding up interventions. This approach is particularly effective for assisted maintenance, where an expert can guide an operator remotely.
Virtual reality immerses users in a fully simulated environment, ideal for technician training and process optimization. Thanks to this technology, high-risk situations can be simulated, enabling operators to learn how to manage breakdowns or incidents without exposing the company to costly production stoppages.
Use cases
- Immersive training of technicians on complex machines prior to actual operation.
- Remote-assisted maintenance with superimposed instructions.
- Precision assembly with real-time guidance.
- Simulation of dangerous situations to improve safety without real risks.
8. 5G: ultra-fast connectivity for industry
Theadoption of 5G in industry enables instant communication between machines, sensors and IT systems. Thanks to its low latency and high bandwidth, it facilitates advanced applications such as remote control of equipment, assisted maintenance and intelligent automation of industrial processes.
One of the main advantages of 5G lies in its ability to manage critical communications thanks to features such as networkslicing. This technique enables the creation of several virtual networks on a common physical infrastructure, each optimized for specific applications, thus guaranteeing end-to-end quality of service and security.
In addition, 5G facilitates the integration of technologies such as augmented reality (AR) and virtual reality (VR) in industrial environments. It also enables the deployment of autonomous vehicles and collaborative robots (cobots) in factories, optimizing logistics flows and production.
Use cases
- Autonomous vehicles in the warehouse to optimize internal logistics.
- Maintenance operations in augmented reality thanks to a high-speed connection.
9. Edge Computing: local data processing for greater responsiveness
Edge Computing revolutionizes industrial data management by processing information directly at source, i.e. at machine and sensor level, rather than sending it to a remote server or cloud. This reduces latency, improves system responsiveness and cuts bandwidth requirements.
In industrial environments where rapid decision-making is crucial, such as automated production lines or the management of critical equipment, Edge Computing enables operations to be optimized in real time, guaranteeing greater system security and resilience in the event of network failure.
Use cases
- Improved cybersecurity by limiting the transfer of sensitive data to external servers.
- Optimize machine performance by adjusting parameters in real time.
10. Blockchain: enhanced traceability and security in industry
Known for its role in the financial sector, blockchain is now finding major applications in industry. This secure, unforgeable information storage and transmission technology reinforces the integrity and traceability of data from the industrialInternet of Things (IoT ). By immutably recording the information generated by machines and sensors, blockchain guarantees that this data has not been altered, thus addressing growing concerns about the reliability and legitimacy of the information collected. It also enhances product traceability, guarantees theauthenticity of materials and strengthens trust between industrial partners.
In complex supply chains, where materials and components pass through numerous intermediaries, blockchain offers total visibility over the origin and route of goods. It also helps reduce fraud and counterfeiting, while facilitating compliance audits.
Use cases
- Enhancing the reliability and traceability of data from theInternet of Things
- Real-time tracking of materials and components throughout the supply chain.
- Automatic product certification to guarantee compliance with standards.
Industry 4.0: a future shaped by technological innovation
Industry 4.0 is evolving at a breakneck pace, thanks to new technologies that optimize production, logistics and resource management. Fromartificial intelligence to indoor geolocation, augmented reality and the Digital Twin, these innovations offer industrial companies a major competitive lever.
Sources and useful links
- Wikipedia - Industrial Internet of Things (IIoT)
- L'Usine Nouvelle - Connected objects at the heart of Industry 4.0
- BPI France - How AI will transform industry
- Industry 4.0 - digital twin
- BPI France - Additive manufacturing (3D printing): what applications for tomorrow's industry?
- Techniques de l'ingénieur - Cobots at the service of all manufacturers
- JDN - Industrie 4.o: augmented reality is already redefining remote assistance
- McKinsey - Smarter Factories: How 5G can jump-start Industry 4.0
- Industrie40.fr - Edge computing
- Lemonde informatique - Industrie 4.0 & IoT: ensuring data integrity through blockchain
Did you like it?
Share it and discover other articles you might also like!
- News
- News
- Articles
An answer