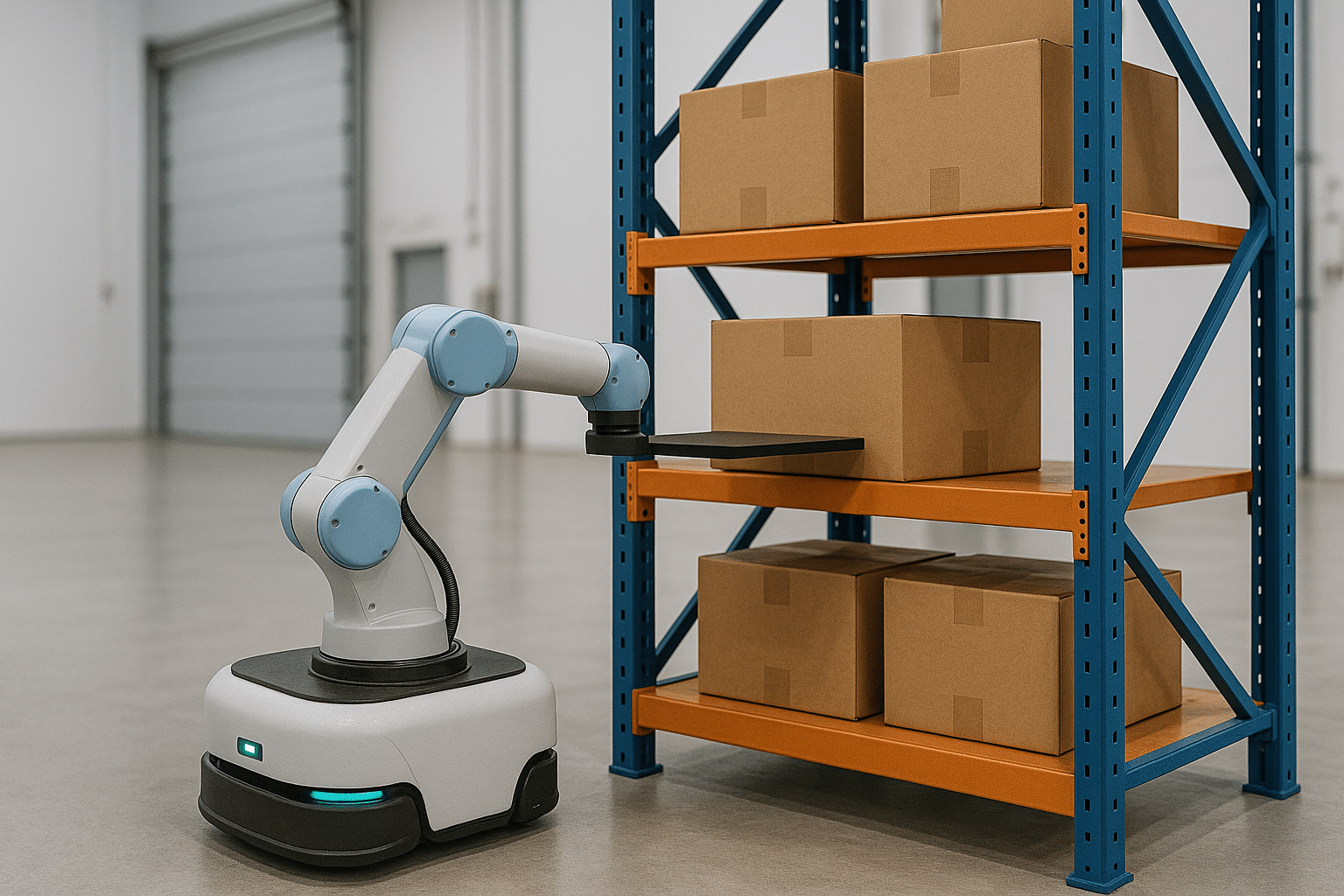
Automatisation industrielle : les 5 principaux défis rencontrés sur le terrain
Partager l'article
Sommaire
Partager l'article
Défi n°1 – Gérer la variabilité des environnements industriels
L’automatisation DE L'industrie face aux réalités du terrain
L’automatisation de industrielle a longtemps reposé sur des environnements stables et prévisibles, conçus pour maximiser la répétabilité des tâches. Mais sur le terrain, la réalité est bien différente : fluctuations de commandes, reconfigurations fréquentes, retards logistiques ou aléas techniques viennent régulièrement perturber les flux établis.
Dans ce contexte, un système automatisé trop rigide devient rapidement source de blocages. C’est l’un des défis majeurs identifiés dans les sites industriels qui cherchent à automatiser tout en conservant une capacité d’adaptation aux changements quotidiens.
Exemple : AMR désorientés en environnement variable
Dans une usine de production de pièces automobiles, les équipes ont déployé des robots mobiles autonomes (AMR) pour alimenter les postes de travail. Initialement, ces robots suivaient des itinéraires fixes, adaptés à une configuration logistique standard.
Mais dès qu’une commande urgente impose un réagencement temporaire des bacs ou des postes, les AMR se retrouvent en échec : itinéraires invalides, points de livraison déplacés, missions non accomplies. Résultat : flux interrompu, files d’attente, perte de cadence.
Ce type de dysfonctionnement illustre bien les limites d’une automatisation industrie pensée en silo, sans capacité d’adaptation dynamique.
Solution : des systèmes interconnectés ET RÉACTIFS
Pour dépasser cette rigidité, l’entreprise a opté pour une approche plus résiliente, fondée sur trois leviers :
Des capteurs en temps réel, pour capter les modifications de l’environnement (positions des bacs, occupation des zones, trajets obstrués).
Une logique embarquée dans les AMR, capable de recalculer les itinéraires et de re-prioriser les missions selon le contexte.
Un orchestrateur robotique connecté à l’ERP, jouant le rôle de tour de contrôle : il synchronise les flux logistiques avec les priorités de production, tout en pilotant l’adaptabilité des robots en temps réel.
Grâce à cette architecture distribuée, les systèmes automatisés ne sont plus figés : ils s’ajustent en continu aux aléas du terrain, tout en restant alignés avec les objectifs opérationnels.
Pour que l’automatisation industrielle fonctionne durablement, elle doit être pensée comme un système vivant, capable d’absorber les imprévus sans rupture de flux.
L’intégration de technologies adaptatives – capteurs, intelligence embarquée, middleware interopérable – devient la condition indispensable pour automatiser des environnements industriels complexes, où la stabilité n’est jamais acquise.
Défi n°2 – Intégrer des systèmes hétérogènes et interopérer avec l’existant
L’hétérogénéité : un frein structurel à l’automatisation industrie
L’un des écueils les plus fréquents dans les projets d’automatisation industrie concerne la cohabitation entre équipements anciens et nouvelles technologies. La plupart des sites industriels ont accumulé, au fil des ans, une infrastructure composée de machines, automates et logiciels de générations variées, souvent incompatibles entre eux.
Dans ce contexte, automatiser ne signifie pas seulement ajouter des capteurs ou des robots : cela implique d’assurer une communication fluide entre les systèmes existants et les briques technologiques récentes.
Exemple : absence de dialogue entre contrôle qualité et ligne automatisée
Une entreprise de l’agroalimentaire souhaitait automatiser le contrôle qualité en intégrant une caméra intelligente sur une ligne de conditionnement. Problème : le convoyeur, piloté par un automate programmable ancien, ne permettait pas de synchroniser les arrêts nécessaires à l’inspection visuelle. Résultat : image floue, défauts non détectés, perte de fiabilité.
Solution : une couche d’interopérabilité entre OT et IT
Pour surmonter cet obstacle, l’équipe projet a mis en place une passerelle de communication OPC-UA/MQTT, permettant d’établir un pont entre le système d’automatisme existant et les nouveaux dispositifs connectés.
Cette approche a permis :
D’exploiter les données de l’automate sans modifier l’infrastructure.
De synchroniser précisément les arrêts du convoyeur avec la prise d’image.
D’intégrer cette nouvelle brique dans un environnement d’automatisation cohérent, sans rupture technologique.
L’interopérabilité est un prérequis essentiel dans tout projet d’automatisation industrielle. Sans elle, les investissements sont fragmentés, les outils restent sous-exploités, et les gains attendus ne sont jamais pleinement réalisés.
Défi n°3 – Exploiter et structurer la donnée en environnement de production
L’automatisation industrieLLE ne fonctionne pas sans maîtrise des flux de données
Capteurs, systèmes de supervision, machines connectées : dans l’industrie 4.0, chaque composant génère des volumes massifs de données. Mais trop souvent, ces données sont silotées, non exploitables, ou analysées avec retard. Une automatisation industrielle efficace suppose donc une architecture de données conçue pour la performance temps réel et l’aide à la décision.
Exemple : une mine d’informations inutilisée dans la logistique interne
Dans un entrepôt de distribution de composants électroniques, les convoyeurs, capteurs de présence, balances et scanners généraient des milliers d’événements chaque jour. Pourtant, aucune alerte ne permettait de détecter les ralentissements ou blocages. Le pilotage se faisait à l’aveugle.
Solution : edge computing et visualisation opérationnelle
La mise en place d’un système de traitement local (edge computing) a permis d’agréger les données critiques (temps d’attente, poids, taux de chargement) pour :
Détecter les anomalies en temps réel.
Afficher un tableau de bord dynamique pour les chefs de ligne.
Alimenter les algorithmes de planification et de maintenance prédictive.
Cette approche a transformé les données dormantes en leviers d’action immédiats, améliorant la réactivité de l’ensemble du système automatisé.
Dans une démarche d’automatisation industrielle, la donnée est un actif stratégique. Sa structuration, son traitement localisé et sa restitution claire font la différence entre une automatisation passive et un pilotage intelligent des opérations.
Défi n°4 – Localiser précisément les actifs, les machines et les opérateurs
La géolocalisation indoor : une brique indispensable pour automatiser sans friction
De nombreux processus automatisés reposent sur la coordination d’éléments mobiles : robots, chariots, postes temporaires, opérateurs. Dans ce contexte, l’automatisation industrielle dépend étroitement de la capacité à localiser ces éléments en temps réel, avec une précision fiable. Sans cela, la logistique interne se désorganise, les systèmes se bloquent, les délais s’allongent.
Exemple : confusion dans la distribution des pièces en atelier
Dans une usine d’assemblage électronique, les AGV de livraison étaient désorientés dès que les postes étaient déplacés pour répondre à une urgence de production. Les missions échouaient, les opérateurs devaient reprendre les flux manuellement.
Solution : intégration de la solution de géolocalisation indoor Wheere
Pour résoudre ces dysfonctionnements récurrents, l’entreprise a déployé la solution de géolocalisation indoor développée par Wheere.
Grâce à une technologie de localisation précise et temps réel, Wheere a permis de :
Localiser en continu les postes de travail, les AGV et les opérateurs avec une technologie adaptée aux environnements industriels à forte densité de métal et de mouvements.
Mettre à jour automatiquement les points de livraison utilisés par les systèmes automatisés, sans intervention manuelle.
Fluidifier la coordination entre logistique automatisée et production, même lors de réorganisations à chaud ou d’urgences opérationnelles.
La plateforme Wheere Cloud s’est interfacée directement avec le WMS et l’outil de pilotage des AGV, permettant une gestion unifiée des flux et une réactivité accrue sur l’ensemble de la chaîne.
Pour garantir la performance de l’automatisation industrielle dans des environnements en constante évolution, la géolocalisation indoor doit être considérée comme une infrastructure de base, au même titre que les capteurs industriels ou les automates. Elle conditionne la fluidité des flux, la fiabilité des interactions entre systèmes, et la capacité des équipements à s’adapter en temps réel.
Cet article pourrait également vous intéresser :
Les 10 innovations technologiques qui révolutionnent l'industrie
Défi n°5 – Accompagner les équipes dans la transformation industrielle
L’humain, pivot de l’automatisation industrie réussie
Même les systèmes les plus avancés restent dépendants de leur intégration dans l’organisation humaine. Trop souvent, les projets d’automatisation industrie échouent non à cause d’un défaut technologique, mais d’un manque d’appropriation par les équipes. La dimension humaine est donc centrale : formation, communication, adaptation des rôles, co-construction sont des leviers de réussite.
Exemple : rejet d’un cobot sur une ligne de productio
Dans une fonderie, l’introduction d’un bras robotique collaboratif devait soulager les opérateurs d’une tâche pénible. Mais par manque d’explication, les équipes l’ont perçu comme une menace ou une source de complication. Résultat : le robot restait à l’arrêt, les tâches étaient effectuées manuellement.
Solution : formation active et co-conception des flux
L’équipe projet a revu son approche :
Formation terrain des opérateurs à l’usage du cobot.
Intégration de leurs retours dans la programmation des trajectoires et la définition des zones de travail.
Valorisation du rôle humain dans la supervision et l’optimisation du poste.
En quelques semaines, l’acceptation du robot est devenue totale, et sa valeur ajoutée pleinement exploitée.
Réussir une stratégie d’automatisation industrielle, c’est aussi repenser la place des collaborateurs, non comme des exécutants mais comme des acteurs augmentés. L’humain n’est pas l’obstacle : il est la clé de voûte.
Vous avez aimé ?
Partagez-le et découvrez d’autres articles qui pourraient également vous plaire !
- Articles
- News
- News